Advanced composites have become indispensible resource in variety of fields including energy. They, for instance, have direct impact in the sector as the efficiency and performance of wind turbine based clean energy technology can be elevated by their optimal use. Nevertheless, advanced composites enable lighter structures for energy-efficient vehicles of transportation without sacrificing the safety. Their undeniable potential calls engineers and scientists to push the boundaries of broad composites research and development for making them even more competitive and promising for stringent energy needs of the society. That is, we are urged to “think outside the box” practices with advancing manufacturing and characterization techniques and software specialized on composites as opposed to traditional lay-ups, materials and production. In the context of multi-scale engineering of composites, a couple of THINKCOMPOSITE concepts that can be implemented in the design of wind turbine blades and structures of vehicles is explored.
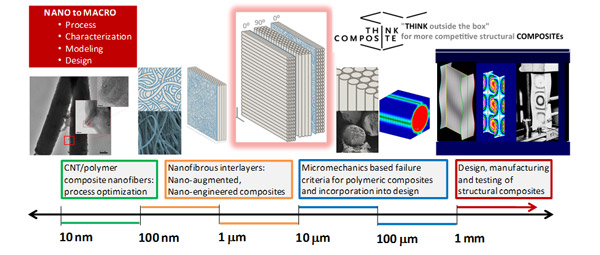
Nano-enhanced/augmented structural compo-sites
The concept realized by nanofibrous inter-layers may find extensive use in nearly all light-weight structural applications, where advanced composites are necessary, such as in aerospace, automotive and energy. They can be easily incorporated into existing manufacturing processes and provide substantially enhanced properties, while the weight and thickness increase associated with interleaving is nearly negligible. Additionally, with the possibilities for combining the right selection of particles/fillers, the toughening performance can be further enhanced for both in- and out-of-plane loading conditions. Moreover, their full potential is even higher with multi-functional possibilities, such as tuning of mechanical, thermal and electrical properties by the right choices of nanofiber and filler combinations and proportions. With a complete understanding of impact on properties by using the nanofibrous interlayers, the opportunities are plentiful for developing characterization and scaled-up production capabilities and integration of the nanofibrous materials into conventional composite engineering design frameworks.
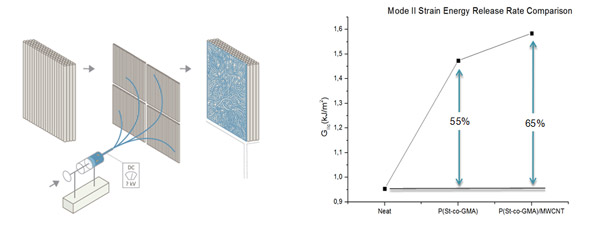
Design of and with non-crimp fabric (NCF) as building blocks for composites
New generation non-crimp fabric (NCF) offers an attractively thin and lightweight building block alternative in the design of composite materials and structures. Pre-assembly of multiple plies of parallel fibers, each laying in a different orientation would not require crimping of the fibers and would enable a one-axis lay-up that can substantially reduce the labor, scrap and manufacturing costs. A state-of-the-art tow-spreading technique enables ply thickness to be reduced to as low as one-third of the typical commercial high quality pre-preg ply thickness. Bi-angle thin-ply NCF offers two different fiber orientations (with one being off-axis) and designing in anisotropic properties within the conventional one-axis ply thickness. In our quest for simultaneous weight and cost reduction at maximum performance of composite structures, the thin-ply bi-angle NCF building block incorporates the simultaneous design of anisotropic properties and structure, as opposed to more traditional composite designs, which typically imitate metals or materials with isotropic behavior.
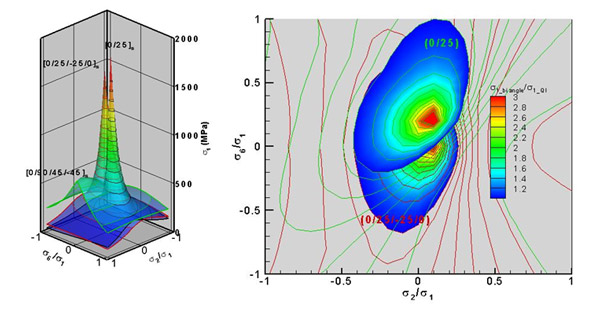