Fume hoods are used to prevent hazardous and odorous chemical exposure release to laboratory, laboratory users and the user. Another substantial reason is limiting spill-affected area within hood and exhausting affected air. Inward air flow through the hood minimized material leakage out of the hood.
Fume hoods are substantial infrastructure element for handling hazardous materials . They should not be misused for the purposes such as garbage, storage of materials, equipment.
A fume hood should be used if a proposed chemical procedure exhibits any one of the following characteristics:
- Airborne concentrations might approach the action level (or permissible exposure limit) (see SDS from ChemWatch)
- Flammable vapors might approach one tenth of the lower explosion limit (see SDS from ChemWatch)
- Materials of unknown toxicity are used or generated
- The odor produced is annoying to laboratory occupants or adjacent units
Procedures that can generally be carried out safely outside the fume hood include those involving the following:
- Water-based solutions of salts, dilute acids, bases, or other reagents
- Very low volatility liquids or solids
- Closed systems that do not allow significant escape into the laboratory environment
- Extremely small quantities of otherwise problematic chemicals. The procedure itself must be evaluated for its potential to increase volatility or produce aerosols.
The fume composed of several elements which are given below:
Face – The face of the hood is the space where air capture occurs.
Sash – The sash is the glass “window” that moves through the hood face to protect the user and laboratory for the period of time in use.
Baffles – The baffles are positioned behind the hood and direct air in the suitable direction. The baffles can also be regulated according to altering vapor densities of chemicals (heavier than air and lighter than air).
Duct – The hood and the ventilation system is attached by the duct and it exhausts to the open air.
Air foil – The air foil is positioned at the bottom front edge of the hood and is a vent that keeps a minimum gap open at all times but more importantly gives aerodynamic properties that allow better, less turbulent air flow and better capture.
In specialized cases, fume hoods will contain exhaust treatment devices, such as water wash-down for perchloric acid use, or charcoal or HEPA filters for removal of particularly toxic or radioactive materials. Fume hoods must not be used for work with infectious agents.
Types of Hoods
Variable Air Volume (VAV) – VAV hoods maintain a constant velocity as the sash moves but changes the volume of air. This can be done by a variety of methods including changing motor speed or closing or opening baffles in the duct. Decrease in air usage at lower sash height provides huge amount of energy savings on heating and cooling.
Standard or Bypass – Air volume varies according to the movement of the sash so that as the sash lowered the velocity decreases. Even bypass hoods have similar design but they have an additional vent at the tpo so that as the sash lowered and the sash space is closed, top vent is simultaneously activated, even though the sash opening is getting smaller, the proportion of air volume flowing through the face is smaller and the velocity remains more constant. Although, performance of bypass hoods are better than standard hoods, they are worse than standard hoods in context of energy saving.
Auxiliary Air – These hoods additional air-injecting blower at the face of the hood. Auxiliary air type hoods are out-of-use owing to their lower performance than VAV and bypass hoods.
Ductless hoods – These hoods are not ducted to outside air but remove contaminants from the air and return it back to the room. HEPA filter, carbon adsorption or catalyst reaction filter may remove the contaminants. Filters should be used in recommended time of use given by the manufacturer. Appropriate filter choice according to your contaminant also plays important role. It is quite important that these elements work properly since the air is reticulated and exposure is eminent. Filter selection and proper working condition must be conducted by LS/LSS. LS/LSS should also consult with laboratory users to evaluate each chemical used in that hood. New chemicals should be informed to LS/LSS for evaluation. Unless the benefits outweigh the hazards and inconvenience because potential for problems, ductless hoods could pose danger. Also, ductless hoods are not indicated when using many liquid, non-aqueous chemicals since the vapors of these chemicals are heavier than air and ductless hoods do not generally have a rear baffle. As a general rule the use of ductless hoods is not recommended.
Clean hoods – Clean hoods are sometimes called laminar hoods but these are different from the type of hood mentioned below.
Design of these hoods are based on preventing the work area with HEPA filtered air from contamination. High incidence of air drawn to the hood is filtered and drop gently from the top of into the work area and small percentage (%10) is drawn through the face of the hood. Face velocities of clean hoods are lower than other hoods, however, the hood is designed to capture with high performance in this form. Due to this capture capability, it is important to have a visual capture test (such as a dry ice test) done on these hoods at least annually.
General Rules Regarding Laboratory Fume Hoods
Before using a fume hood:
- Measure the level of hazard declared by the material involved and use only hoods that have appropriate face velocity.
- Confirm that the fume hood is operational by testing the tell-tale (paper hanging from hood sash) periodically and air monitoring device if the hood is fitted with one. If there is no indicator, difficulty in visualizing, or not functioning, place a piece of paper to the sash in an area where it will not prevent the ongoing processes.
- If the fume hood is out of service, the fume should not be used under any circumstances.
General operational rules:
- Always work with the fume hood sash as low as possible (no higher than 50 cm). Low hood sash working increases the performance of the hood. Low sash position is not only energy saver but also have safety shield property during experiments.
- For optimum performance of the fume hood, There should be at least 15 cm distance between materials and face of the vents or baffle openings in the back of the hood should not blocked in any case (Figure 4.1).
- Any lab apparatus should be raised at least 2.5 cm above the work surface of the hood to improve airflow in the hood. Bench stands or items such as blocks, metal test tube racks, or other items that will not react with the chemical(s) in use should be used (Figure 4.2).
- Windows and doors should be kept closed within the lab and minimize traffic in front of the hood when the hood is operational. Quick movements should also be reduced while working in the hood, including opening and closing the sash. These steps mentioned above will help to prevent air currents, which can result in hazardous vapours being leaked from the hood and into the laboratory users’ working area.
Other considerations:
- Fume hood should not used for evaporation of hazardous waste.
- For particularly hazardous substances or chemicals that can form toxic vapours, fumes, or dusts, the hood or equipment within the hood may have to be tailored with condensers, traps, or scrubbers in order to prevent the vapours, fumes, and dusts from being leaked into the laboratory area.
- Flammable liquid including containers must be grounded and interconnected each other while transferring these liquids to another container. Static electricity generation could lead to ignite these liquids abruptly.
- In case of chemical spill, area should be cleaned immediately or reported to LS/LSS if the volume of spill could not be handled easily. Working area and hood sash should be washed frequently and always be preserved a clean, dry and ready-to-work area.
- Only hands should be inside of the hood. Never put your head inside a functioning laboratory hood to monitor an experiment.
- The plane of the sash is the border between contaminated and uncontaminated zone. The sash must always be between the user and hood contents.
- All the equipment and other apparatus such as bottles, beakers, unrelated materials etc. should not be stored or located in the hood, hence the hood area is limited. If there is grill along the bottom slot or baffle in the back the hood, it also should be kept clean.
- Actively used materials could be allowed to place in the hood. Extraneous chemicals left in an active hood can contribute to a fire or explosion.
- Elevate any equipment that needs to remain in hoods on racks or feet to provide airflow under the equipment.
- Name and other necessary information about lab-responsible students or personnel should be written in a visible location.
- Before the maintenance; all the materials should be removed and cleaned.
- Report suspected hood malfunctions promptly to LS/LSS. If the fume hood is not working properly, let other people in the lab know by hanging up a “Do Not Use” sign on the hood.
- Hoods operation shall be evaluated annually by SU LS/LSS or a qualified third party.
Specifications:
- Operation standard for general purpose hoods is 0.5 m/s ± 10%.
- Operation standard of hoods specialized for highly toxic or carcinogenic materials is 0.6 m/s ± 10%.
- Hoods should not, as a matter of course, operate above 0.75 m/s to prevent the potential for dangerous turbulence that could result in exposure to the user.
- Fume hood sash should be kept closed when you are away from the hood or leave the lab.
- Tampering with fume hoods/fume hood exhaust ducts by adding additional equipment on to the load of the hood or cutting/drilling into exhaust ducts without consulting with LSS is forbidden.
Figure 4.1 and 4.2 show the effect of material placement to working conditions:
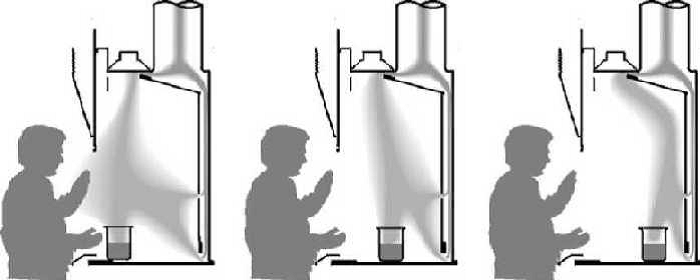
Figure 4.1 Effect of material placement: (L to R) Bad Placement, Good placement, Best placement
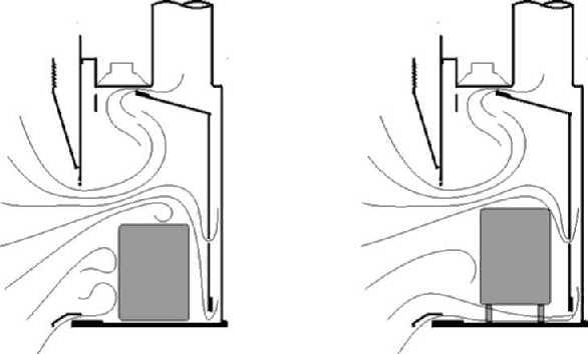
Figure 4.2 Effect of large equipment placement: (L to R) Poor placement, and Good placement
(Courtesy of Dekolab)
Fume Hood Inspection and Testing Program
Annual testing and inspection of fume hoods are coordinated by LS/LSS and performed by the authorized company (manufacturer). The fume hood inspection program consists of a detailed preliminary inspection followed by annual standardized inspections for all fume hoods on campus. This initial inspection will offer baseline information including, but not limited to, hood utilization, category of hood, room and building information, and average face velocity capacities.
Follow-up inspections for appropriate procedure and face velocity (airflow) measurements will be performed on an annual basis and upon request by laboratory users. Upon accomplishment of each inspection, hoods will be categorized with an inspection sticker indicating face velocity, date inspected, and initials of the inspector. File including inspection datas will be kept in database.
Fume hood testing and inspection consist of the following:
- The face velocity will be tested for compliance with EN 14175 standard.
- A visual inspection using dry ice can be volunteered by users or LS/LSS in conjunction with face velocity measurements. Dry Ice Test can be found in the Appendix 4.1.
- If your fume hood is filled with equipment, experimental set up or any material which hinders the test, you will be contacted by LS/LSS for further information before your fume hood can be tested
A fume hood that has not passed the authorized company inspection and has a warning sign attached, even if the fume hood appears to have airflow is not allowed to operate. Laboratory users must arrange or coordinate with other available laboratories with operational fume hoods if their work necessitates the usage of a fume hood.
LSS will coordinate fume hood repairs with the Operational and Technical Services unit to ensure a timely and accurate repair process.
References and sources for information from the relevant websites and documentation of different universities, NGOs and government agencies used in the preparation of this website are provided at references.